「しなやかなタフポリマー」が素材の可能性を拓く
1. はじめに
ポリマー材料の高機能化・高付加価値化、および用途の多様化が進む中、複数の樹脂成分を組み合わせるポリマーアロイによる新素材開発が盛んに行われており、近年では、ナノオーダーでアロイ構造を形成させる技術により、従来からのアロイ技術では達成不可の飛躍的な高性能化を可能とする技術が報告されている1)。
内装、家電製品の筐体などの身近な部材に用いられることが多く、衝突や落下で壊れないタフさが要求される。しかしポリマー材料は、硬い程壊れやすく、柔らかい程壊れにくい特性を有し、柔軟なゴムなどを添加した場合、耐衝撃性は改善されるものの、強度・剛性が低下する課題があった。そして、このポリマー材料が破壊する際には、分子レベルでは、糸毬状に絡み合ったポリマーが、ほぐれながら変形し、最終的に一部分に応力が集中し、分子鎖が切断することで壊れるものと考えられている。すなわち材料中の一部に局所的な応力が集中することで、壊れ易くなり、ポリマー材料が本来持っている性能を十分に発揮しきれていない可能性がある。
ここで、応力印加時に変形を可能とするポリマーとして、分子結合部がスライドし環動ポリマー構造となるポリロタキサンが知られている。ポリロタキサンはリング状の分子をポリマー分子が貫通し、数珠やネックレスのような構造を持ったいわゆる超分子ポリマーである。さらにこのリング状の分子同士を化学結合で結合させたポリロタキサンゲル2)は、分子結合部がポリマー分子に沿ってスライドすることで、応力集中を抑制させるものと考えられている3)。
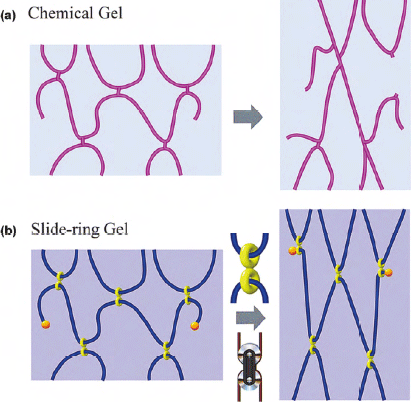
(b)ポリロタキサンからなるゲルの模式図 3)
この様な背景の下、東レでは環状高分子であるポリロタキサンを、種々のポリマー中にナノオーダーで高度に分散させる研究開発を進め、これにより飛躍的な高性能化を実現した各種ポリマー材料を創出した。以下、これらの技術と材料の特徴を紹介する。
2. ポリロタキサン導入ポリアミド6の開発 4)
上述の分子結合部がスライドするポリロタキサンの構造をポリアミド6中に、ナノオーダーで高度に分散させることで、ポリアミド6の元来有する剛性・強度を保ったまま、破断伸びを飛躍的に向上させた革新的な材料を開発した。
検討に際し、まずポリアミド6との親和性を高めるべくポリロタキサンのリング状分子に側鎖をグラフト化し、さらに側鎖の末端には、ポリアミド6との溶融混練時に反応する官能基を付与するなどのポリロタキサンの分子設計を行った。さらにこの変性ポリロタキサンを用い、ポリアミド6とのリアクティブプロセッシングする際に、2種類以上のプラスチックをナノメートル単位で最適に混合する技術である東レのナノアロイ®を適用した結果、ポリアミド6とポリロタキサンの分子同士を結合させることが初めて可能となった。
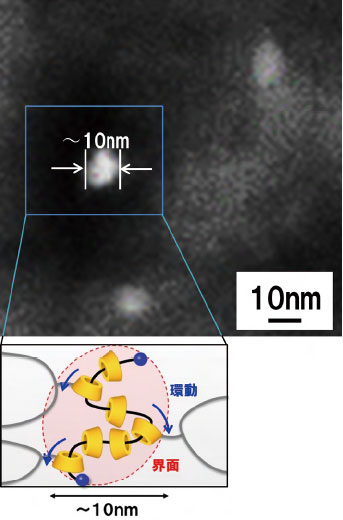
(マトリックス樹脂中に約10nmのポリロタキサン相(白色部)が均一に分散。)
これにより、引張試験における破断伸びは環動ポリマー構造を組み込まない場合と比較して、約6倍に向上し、さらに繰り返し曲げ試験における屈曲耐久性を、約20倍と大幅に向上させることが可能となった。剛性、強度を保ったまま、これら特性を向上させた材料は、従来の、柔軟材料を添加する手法では得られない。さらに、箱状成形品を用いた衝撃試験では、ポリロタキサンによる環動ポリマー構造を組み込むことで、破壊されにくくなり、約2倍強のエネルギー吸収性を示すことがわかった。
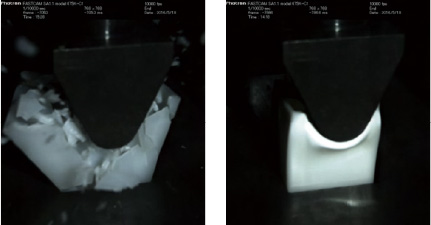
(高さ2mからおもりを落下。ポリアミド6は破壊(左図)したのに対し、開発材料は変形しながらエネルギーを吸収(右図)した。)
ポリアミド6にポリロタキサンを導入すると、ポリアミド6と比較し大きなクラックが発生することなく変形可能であり、この様な特性発現の機構解明のため、大型放射光設備(SPring-8)を用いた引張in-situ SAXS測定から、変形時には数10ナノメートルの大きさの微細なボイドを形成しながら大きく変形していることが初めて判明した。この様なボイドの形成は、分子結合部がスライドする環動ポリマー構造がポリアミド6に組み込まれたことと密接に関係していると考えており、本構造により剛性、強度を保ちながら大きく柔軟に変形することが可能となったものと推定している。
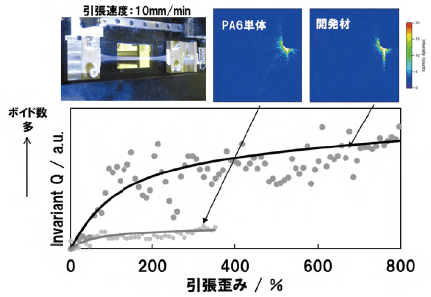
3.ポリロタキサン導入ガラス強化系ポリアミド6の開発 4)
一般的に、強度と剛性を高める目的で、ガラス繊維や炭素繊維で複合化した繊維強化ポリマーは、大幅な補強効果が得られる反面、繊維方向の強度と比較して、繊維に垂直方向にかかる剥離強度が低いため、繊維表面が破壊の起点となり、大きな変形に追随できず、複合材料においても脆く壊れやすくなることが課題であった。
この様に、ポリマー系の複合材料においても、破壊の起点となる繊維表面に分子結合部がスライドする環動ポリマー構造を選択的に配置することできれば、ポリロタキサンのもつ “加えられた力を分子レベルで「いなす」効果” を発揮することができるのではないかと考えた。
そこで、分子結合部がスライドするポリロタキサンをポリマーと繊維の境界面に選択的に配置することで、従来の繊維強化ポリマーでは困難であった強度と靱性の両立に成功した。
本検討では、ポリロタキサンの分子設計に加え、繊維表面をポリロタキサンとの親和性が高くなる様、専用設計することで、繊維表面に高濃度のポリロタキサンを選択的に配置させ、変形時に受けた力を繊維表面で「いなす」ことで、繊維強化プラスチックのもつ高剛性、高強度を保ちながら、高靱性化を実現した。
本技術をポリアミド6に適用することで、材料の破断伸びは環動ポリマー構造を組み込まない場合と比較して、実に5倍以上の15%超にまで向上し、さらに、箱状成形品を用いた衝撃試験では、環動ポリマー構造を組み込むことで、全く異なる破壊形態となり、4倍以上のエネルギーを吸収することがわかった
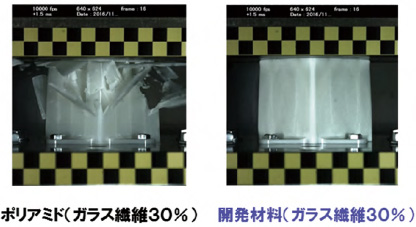
(250kgの錘を、高さを変えて落下させることで、入力エネルギーを設定。ポリアミド6(ガラス繊維30%)は破壊(左図)したのに対し、開発材料(右図)は変形しながらエネルギーを吸収。)
このような特性発現機構の詳細については、TOF-SIMS(飛行時間型2次イオン質量分析法)による繊維表面の成分分析から、開発材では、繊維表面に高濃度のポリロタキサンが存在することが判明しており、繊維表面に分子結合部がスライドする環動ポリマー構造が組み込まれた結果であり、繊維表面のポリロタキサン量を制御することが本技術のキーであると考えている。
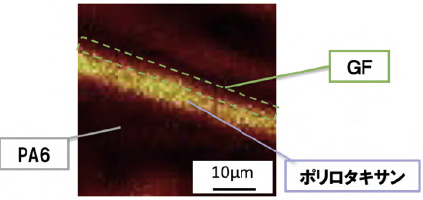
4 .ポリロタキサン導入炭素繊維強化プラスチックの開発 5)
さらに、分子結合部がスライドする環動ポリマー構造を炭素繊維強化プラスチック(以下、「CFRP」:Carbon Fiber Reinforced Plastics)に導入することで、CFRPの耐疲労特性を向上させる新たなポリマーアロイ技術を開発した。
ここでCFRPのマトリックス樹脂として用いられる熱硬化性樹脂は、分子内に架橋点を持つことから、熱可塑性樹脂と比較して優れた強度・剛性を示すが、架橋点により分子の動きが制限されることで、材料の変形に追随できず、繰り返しの変形により壊れやすくなる懸念があり、耐疲労特性向上によるさらなる高性能化が期待されていた。
CFRPにおいて熱硬化性樹脂の耐疲労特性を向上させる方法として、靱性に優れるゴム成分の配合が知られているが、ゴムは、弾性率やガラス転移温度が低いため、ゴム成分の配合により、樹脂硬化物の弾性率が低下し、耐疲労特性と剛性、強度のバランスを取ることは困難であった。
本検討では、ポリロタキサンをCFRPのマトリックス樹脂である熱硬化性樹脂中にナノスケールで均一に分散させることに取り組み、具体的には、分子設計技術に基づきポリロタキサンの分子構造を最適化した上で、熱硬化性樹脂の出発原料である低粘度の低分子量化合物(プレポリマー)とポリロタキサンを攪拌、混合、溶解し、分子レベルで均一な相溶混合物とした後、重合の化学反応で生じる相溶性変化を利用することで、ポリマーアロイ構造をナノレベルで高度に制御することに成功した。
この様に合成した熱硬化性樹脂をCFRPのマトリックス樹脂として使用した結果、一般的なCFRPが有する高強度、高剛性を保ちながら、繰り返し曲げ疲労試験において、環動ポリマー構造を組み込まない場合に比べ、耐疲労特性を約3倍にまで向上させることに成功した。
また透過型電子顕微鏡による観察から、熱硬化性樹脂中にポリロタキサンがナノメートルオーダーで均一に存在することを確認している。このことから、相溶状態から硬化させて、ポリロタキサンを架橋点に均一に配置させることが本技術のキーであると考えられる。さらにポリロタキサンがナノメートルオーダーに均一に分散させた熱硬化性樹脂の大変形後の透過型電子顕微鏡による観察の結果、ナノ分散したポリロタキサンを起点に、万遍なく微細なクラック(1μm程度)が形成されていることも確認している。
この様に、熱硬化性樹脂の破壊の起点となりうる架橋点に分子結合部がスライドする環動ポリマー構造を効果的に組み込み、変形時に受けた力を分子レベルで「いなす」効果を発揮できる分子構造を実現したことにより、今回の耐疲労特性の劇的な向上が達成できたものと考えている。
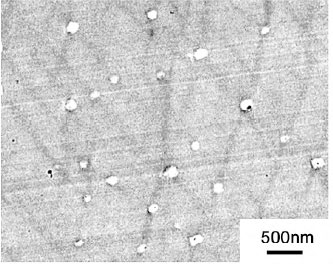
(ナノ分散したポリロタキサン相を起点に、万遍なく微細なクラック(1μm 程度)が形成)
5.おわりに
本研究で開発したポリロタキサンによる環動ポリマー構造の導入技術により、ポリマー、繊維強化ポリマー、CFRPの持つポテンシャルを最大限に引き出せる可能性があることから、自動車、家電製品、スポーツ用品など、幅広い応用展開とポリマー材料市場の拡大が期待される6)。本研究で開発した環動ポリマー構造の各種ポリマーへの導入技術による高性能化が、様々な分野で効力を発揮することを期待している。